
EVAPCO Alcoil Replacement Coils: Carrier 30RB and 30XA
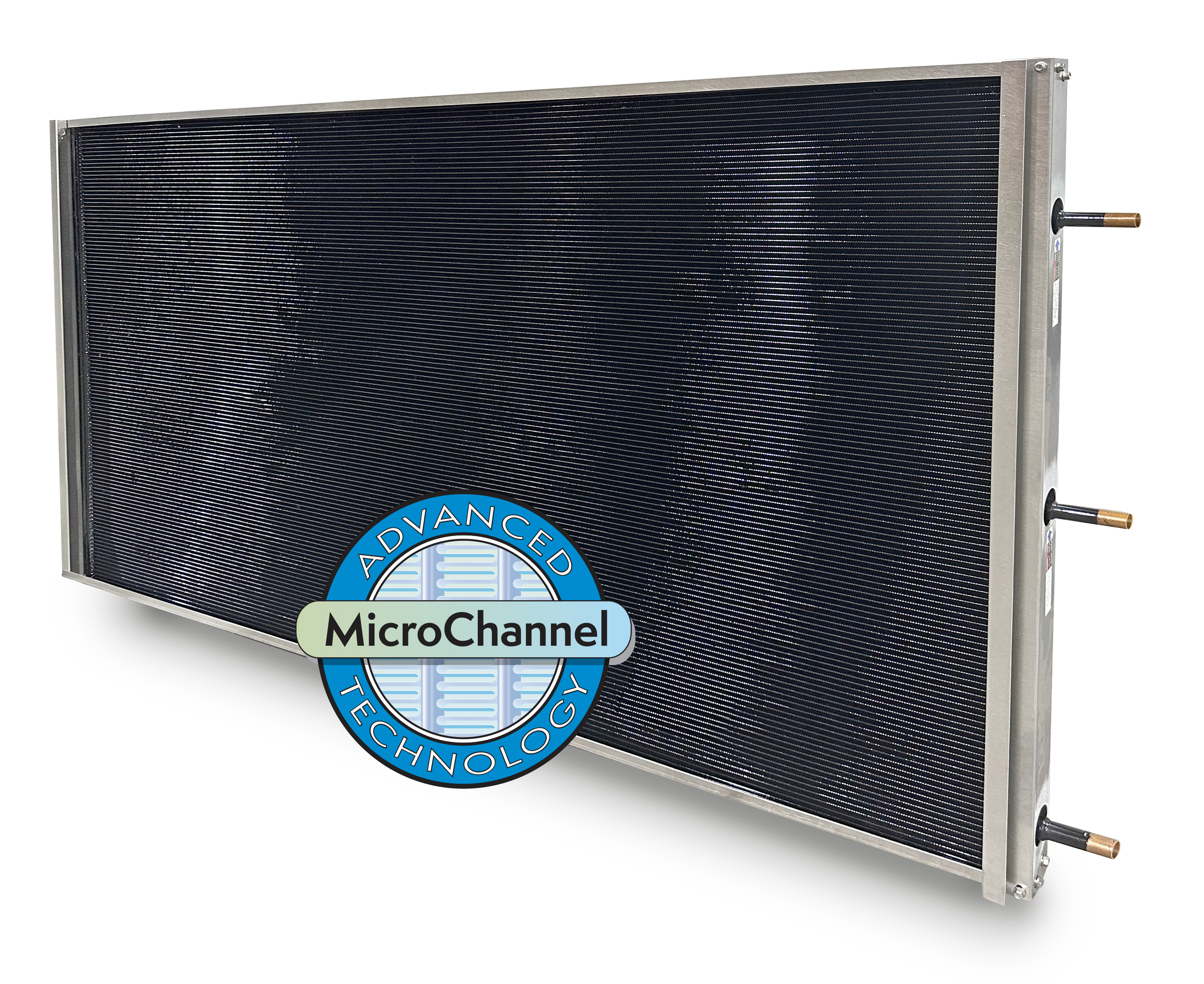
Description
EVAPCO Alcoil manufacturers alternative replacement condenser coils for Carrier brand chillers, specifically for the Carrier 30RB and the Carrier 30XA. These replacement coils are designed as near perfect drop-in, with higher quality, longer life. The coils are 80.5” wide by 44.0” tall by 4” deep and have copper O.D. solder connections and a flange/casing for easy installation.
Key Features
- Available from Stock. Contact factory for availability.
- UL Listed, U.S. & Canada
- Five (5) Year Limited Warranty Against Defects in Materials & Workmanship
- 650 PSI Working Pressure for R410A or R134a Service
- Epoxy Coated for Additional Corrosion Protection
- For MicroChannel and/or Fin/Tube Coil Replacement
- Replacement for PN: 30RB660054, 30RB660055, 00PPG000450800A, 30RB660013, 00PPG000473501A
Comparative Advantages
- Made in the USA
- Proven Performance and Robust Design
- 100% Factory Leak Tested
- Constructed with Long Life Alloy for Extended Service Life
- Designed to Replace Fin/Tube and MicroChannel Coils in Carrier Chillers
The Best Replacement Coil
EVAPCO Alcoil replacement coils are designed as an UPGRADE to the original manufacture’s heat exchanger, either Microchannel type or Fin/Tube type. The heat exchanger is UPGRADED with Long Life Alloy and E-Coating to assure long life corrosion protection. As a primary supplier to major HVAC & Refrigeration Original Equipment Manufacturers, EVAPCO Alcoil leads the industry in MicroChannel heat exchanger Design, Quality, and Customer Service. All EVAPCO Alcoil heat exchangers are made in York, Pennsylvania, USA and are shipped from stock or made to order.
Product Drawing
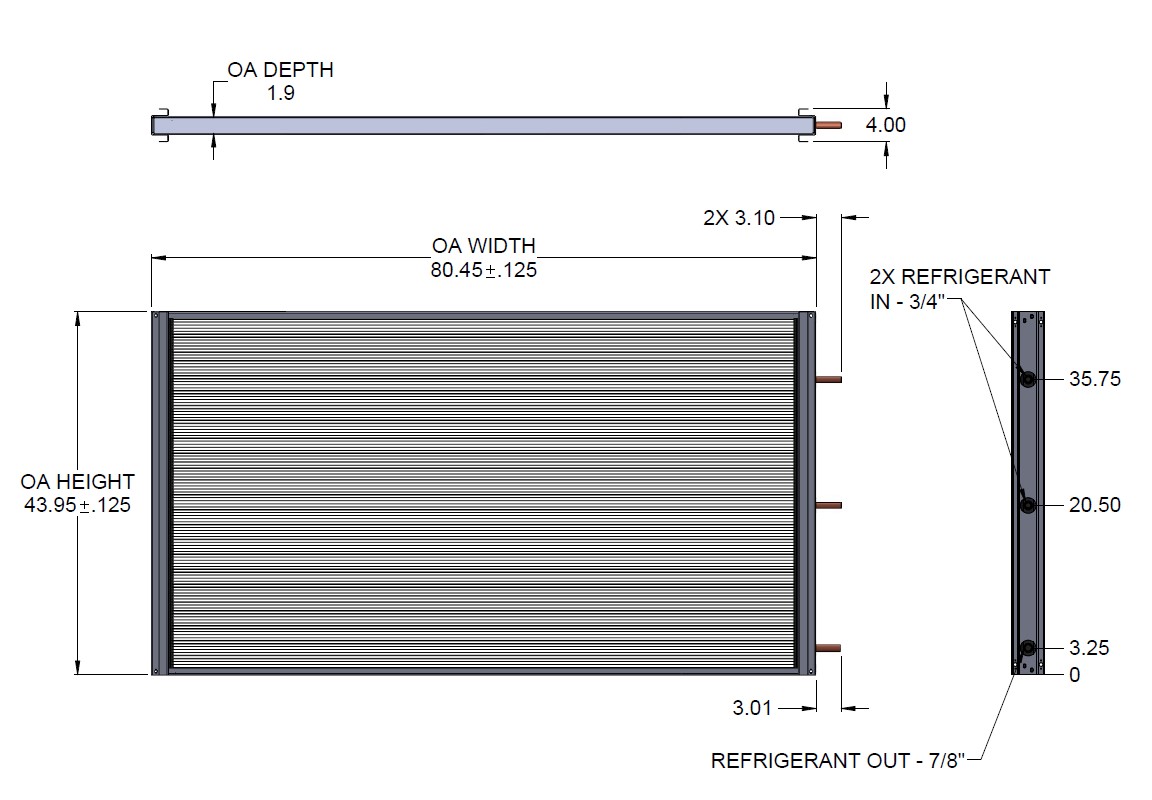
Model: 2C37.8x41x.83V-13K18-P1359C (E-Coated)
E-Coating (Standard for All Carrier 30RB & XA Replacement Coils)
Recommended for corrosive applications such as industrial applications and sea coast environments. Recommended for replacement coils where the previously failed coil shows signs of refrigerant oil spots or leaks on the coil due to corrosion.
- Epoxy Electrocoat, 0.001 Inch Nominal Coating Thickness
- Black, Semi-gloss appearance
- UV Topcoat
Installation Guidelines
- Remove existing coil(s) using standard industry practices and in accordance with refrigerant recovery regulations.
- Install new coils. Condenser inlet connection must be at the top, per the drawing. Do not install upside down. Use care to not damage coil face while handling.
- Two existing 3/4" inlet connections to connect the two 3/4" Inlet connections.
- 7/8" Outlet connection to connect 7/8" Outlet connection.
- Solder copper connections using Silver solder or Phos-Copper method. Use wet rag on Al side of connections to protect the Al/Cu joint from overheating and damage to the Al/Cu joint.
- Replace one or all coils in each compressor circuit.
Leak check all connections. Re-charge the system using the original OEM's recommended refrigerant charge quantity, then adjust using site glass (minimal bubbles) and sub-cooling and 5F to 10F.
Replacement Coil Brochure – Carrier 30RB and 30XA